
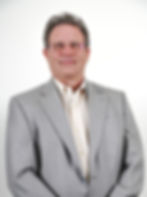
When I was a young man, I worked with my father on remodel projects such as bathrooms, a house addition, kitchen remodel, and building a recreation room. My father was a very organized handyman. He taught me how to stage equipment, get it installed neatly and efficiently, and make the best use of our time.
Fast forward to 2019 and I had a pole barn out near Alvin, Texas (thanks for finding the place Jaime Chapa) and I thought it would be great to take a piece of this barn and make living quarters in it. At the end of 2019 I started drawing up plans to make a 525 square foot living space in a piece of that barn. I did the design drawings, material procurement, staging and construction (with a little help from my friends). I did the work throughout 2020 and moved into the space the first week of December 2020. The punch list is receding and will be finished mid-February 2021.
Starting from scratch, it takes a lot of hours and planning to put something like this together. The work included epoxy floor, electric and plumbing rough-in, bending and installing conduit, installing a new electrical panel, pulling wire, plumbing finish-out, hanging doors, installing wall panels, ceiling installation, closets, cabinets, appliances and lighting fixtures. It came out very well, but in the process, I was reminded of something that can occur on anything custom: Rework.
Rework is what happens when you must remove or revise the work you've already installed. With all of that great work, I figured there is somewhere around 35 hours of rework that I've done. That is almost one man-week and approximately $2,500 to $3,500 in billable hours. What are the reasons for my rework? I'm glad you asked.
Ron’s Rework Fast Five;
1. Measure twice, cut once.
I only had a few problems with this during framing. It remains a mystery why we had to remove some studs and move a window opening on one of the tip-up walls. Luckily, we were in the rough stage on the ground and it could be done easily, but it still cost me time.
2. Work out of sequence.
I had windows on a long COVID back order from Lowe’s that forced me to go back and remove a few interior wall panels to get the windows installed. It cost me six hours. Ouch.
3. Communicate, Communicate, and then verify.
The contractor doing the outside walls installed the entry door right in the center of the space where he thought it should be and not where my drawing showed the door. That meant the plumbing rough-in did not work the way I planned. Part of the rework was installing the washing machine into the central part of the barn so that I could make the plumbing rough-in work for the new bathroom. That simple communication element cost me a half-day of redesign and another day of messing around.
4. What I thought I knew.
When installing paneling, a woodworker always trims at the end. But when doing interior metal aluminum wall panels, I found out that you trim first and install the panels into the trim. I didn't know this so that caused a lot of rework of removing panels, installing to place it into the trim.
5. Nothing good happens after midnight (Bill Parcells).
One culprit for rework is doing late night work when you are tired and aren't seeing everything clearly. Of course, you don’t know this at the time. It is disappointing to come back the next day and have to fix an error from “tired-head” the night before.
Eliminating the need for rework shows our best effort. What things have you reworked lately? How can you avoid rework next time?
Keeping organized and asking questions along the way is the best practice. Our customers can only afford for us to do the job once. Is there someone who can help you get organized or get the sequence fixed? Is there a special tool that will make the job go better? Do you need more sleep?
-Ronald F. Kruse, Chief Operating Officer, Houston